By Jonathan Koffel and Rami Jubara
PLOS One recently published an article about an effective, low cost, 3D printed stethoscope. The researchers found that the 3D-printed stethoscope was comparable to the Littmann Cardiology III — and that it could be made at a $5 price point.
The researchers promote this stethoscope as a promising tool for physicians working in low- to middle-income countries where the cost of a typical stethoscope may present a significant financial barrier. It is part of a larger research project to design open, printable and validated devices ranging from otoscopes to tourniquets to pulse oximeters.
We recently used the open access designs to print a stethoscope in our Makerspace. Here’s what the process looked like and what we learned.
Step 1: Design
The researchers designed the 3D-printed stethoscope components using CrystalSCAD and OpenSCAD, two open source computer-aided design (CAD) tools.
They also made all of the files from the project, from the original models to the printable parts to sound files used to test the stethoscope, freely available via a GitHub repository. This makes it easy for others to customize the parts based on their needs and suggest improvements to the original models.
Step 2: Printing
The parts were printed on the Bio-Medical Library’s Original Prusa i3 Mk3 printer and took about 4 hours to print out of PLA plastic. The non-printed parts (earbuds, silicone tubes, thin plastic sheet) were all generally inexpensive and easy to find.
Each stethoscope uses 57 grams of plastic that cost us $1.72. Although we just printed one copy to start, the researchers have printed up to 3 at a time.
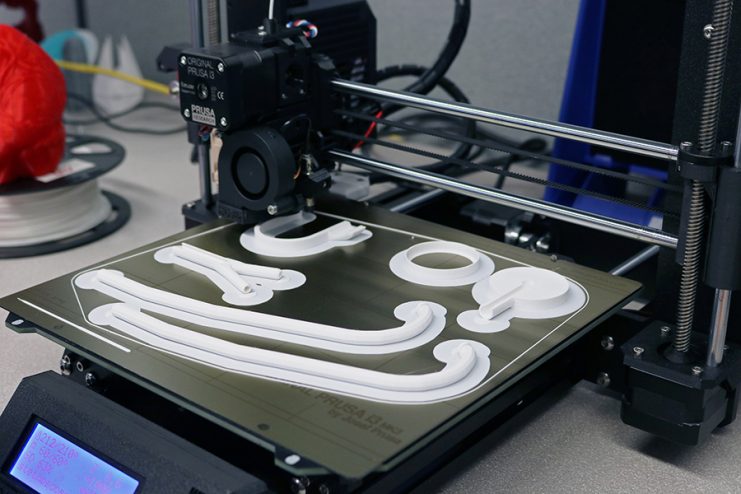
Printing of stethoscope. Photo credit Allison Thompson.
Step 3: Assembly
To assemble the stethoscope, we just connected the pieces using two widths of silicone tubing, slid the earbuds onto the ends of the earpieces, and cut a plastic circle out of a plastic folder to use as a diaphragm in the bell.
When we tested the fit, it turned out that the earpieces were too close together and it really hurt to wear. Ten seconds with a heat gun, however, softened the y-piece connecting the earpieces and we were able to bend it to a much more comfortable width.
One of the great things about 3D printing and open source hardware is that we aren’t stuck with the model we were given — we’re free to open up the files and adjust the parts ourselves so future copies will fit right off the bat!
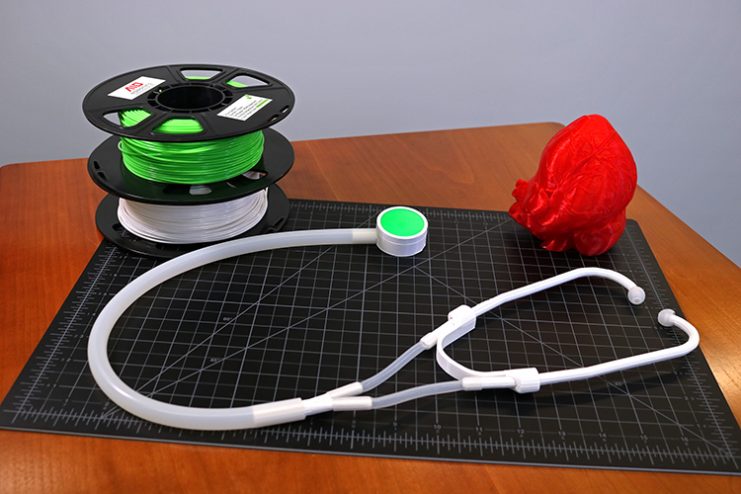
Final Stethoscope. Photo credit Allison Thompson.
Step 4: Use
And best of all, the stethoscope actually works! There will certainly be refinements to the design to make it work better or print more easily, but this is a great start to a less than $5 stethoscope. Also, revisions are easy since the researchers have shared the source files with the world.
Interested in learning more about how 3D printing and other emerging technologies can be used in healthcare? Come to the Bio-Medical Library Makerspace or reach out to us at lib-makerspaces@umn.edu.
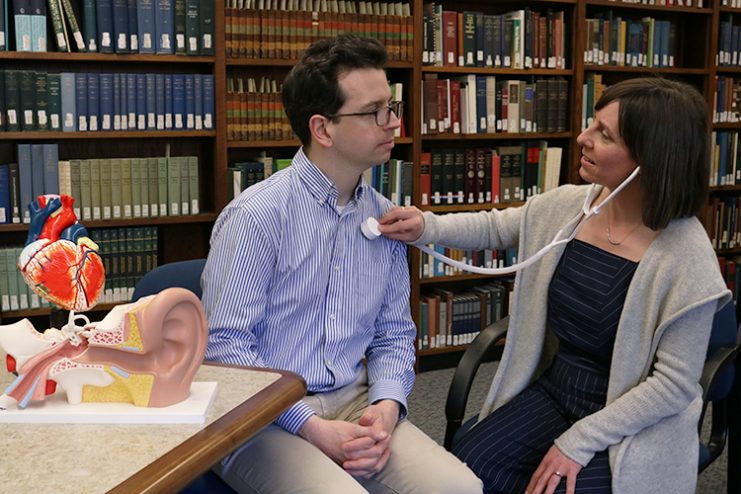
Use of stethoscope. Photo credit Allison Thompson.
About the authors
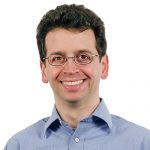
Jonathan Koffel
Jonathan Koffel is an Associate Librarian and leads work in the Health Sciences Libraries around makerspaces, data visualization, virtual reality and the application of emerging tools and technologies to health care and health education.
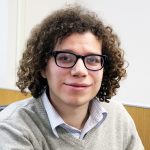
Rami Jubara
Rami Jubara works to support the Bio-Medical Library Makerspace, assisting with – and teaching classes on – virtual reality, 3D printing, and other emerging tech resources and services.